EN/DIN Cold Drawn Black Phosphated precision hydraulic Steel Tube
Product Detail
The black phosphated hydraulic steel tube is produced according to DIN 2391-C or En10305-4. Black phosphated hydraulic steel tubes are made of cold drawn bright steel pipes as the substrate. And the inner and outer walls of the pipes are phosphatized with phosphating solution to form a black phosphating protective film. Absorb rust resistant oil through the micropores in the phosphating film for rust prevention treatment, and cover both ends for dust prevention treatment. The main characteristics of hydraulic black phosphating steel pipes are uniform color, high consistency, and good rust resistance.
Phosphated hydraulic steel tubes are widely used in hydraulic systems, construction machinery and construction vehicles.
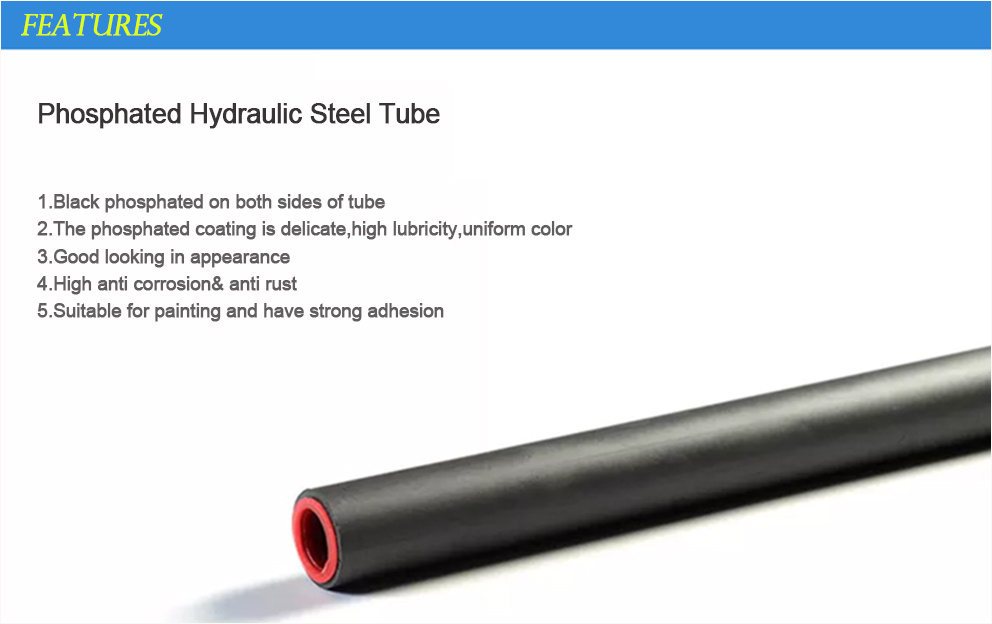
Specification
Standard |
DIN2391 DIN1630 EN10305 DIN2445 JIS G3445 SAE J524 |
Grade |
ST35/E235 ST37.4 ST45/E255 ST52/E355 |
Delivery Condition |
NBK(+N) BK(+C) GBK(+A) BKW(+LC) BKS(+SR) |
Size |
OD:4 to 219mm Thickness 0.5-35mm, Length: 3m,5.8,6 or according to requirements |
Finish |
Galvanized surface (Sliver/Yellow/Colorful) Zinc coating of 8-12um |
Application |
Hydraulic System; Car/bus; construction vehicle |
Delivery time |
A.3 days if this good is stock goods. B. About 30 days according to the quantity |
HYDRAULIC PRECSION STEEL TUBE IN STOCK |
||||||||||
OD |
Thickness(mm) |
|||||||||
mm |
|
|||||||||
4 |
4*1 |
|
|
|
|
|
|
|
|
|
6 |
6*1 |
6*1.5 |
6*2 |
|
|
|
|
|
|
|
8 |
8*1 |
8*1.5 |
8*2 |
|
|
|
|
|
|
|
10 |
10*1 |
10*1.5 |
10*2 |
10*2.5 |
|
|
|
|
|
|
12 |
12*1 |
12*1.5 |
12*2 |
12*2.5 |
12*3 |
|
|
|
|
|
14 |
14*1 |
14*1.5 |
14*2 |
14*2.5 |
14*3 |
|
|
|
|
|
15 |
15*1 |
15*1.5 |
15*2 |
15*2.5 |
15*3 |
15*3.5 |
|
|
|
|
16 |
16*1 |
16*1.5 |
16*2 |
16*2.5 |
16*3 |
16*3.5 |
16*4 |
16*4.5 |
|
|
18 |
18*1 |
18*1.5 |
18*2 |
18*2.5 |
18*3 |
18*3.5 |
18*4 |
18*4.5 |
|
|
20 |
20*1 |
20*1.5 |
20*2 |
20*2.5 |
20*3 |
20*3.5 |
20*4 |
20*4.5 |
20*5 |
|
22 |
22*1 |
22*1.5 |
22*2 |
22*2.5 |
22*3 |
22*3.5 |
22*4 |
22*4.5 |
22*5 |
|
25 |
25*1 |
25*1.5 |
25*2 |
25*2.5 |
25*3 |
25*3.5 |
25*4 |
25*4.5 |
25*5 |
|
28 |
28*1 |
28*1.5 |
28*2 |
28*2.5 |
28*3 |
28*3.5 |
28*4 |
28*4.5 |
28*5 |
|
30 |
30*1 |
30*1.5 |
30*2 |
30*2.5 |
30*3 |
30*3.5 |
30*4 |
30*4.5 |
30*5 |
30*6 |
32 |
|
32*1.5 |
32*2 |
32*2.5 |
32*3 |
32*3.5 |
32*4 |
32*4.5 |
32*5 |
32*6 |
34 |
|
34*1.5 |
34*2 |
34*2.5 |
34*3 |
34*3.5 |
34*4 |
34*4.5 |
34*5 |
34*6 |
35 |
|
35*1.5 |
35*2 |
35*2.5 |
35*3 |
35*3.5 |
35*4 |
35*4.5 |
35*5 |
35*6 |
38 |
|
|
38*2 |
38*2.5 |
38*3 |
38*3.5 |
38*4 |
38*4.5 |
38*5 |
38*6 |
40 |
|
|
40*2 |
40*2.5 |
40*3 |
40*3.5 |
40*4 |
40*4.5 |
40*5 |
40*6 |
42 |
|
|
42*2 |
42*2.5 |
42*3 |
42*3.5 |
42*4 |
42*4.5 |
42*5 |
42*6 |
45 |
|
|
45*2 |
45*2.5 |
45*3 |
45*3.5 |
45*4 |
45*4.5 |
45*5 |
45*6 |
46 |
|
|
46*2 |
46*2.5 |
46*3 |
46*3.5 |
46*4 |
46*4.5 |
46*5 |
46*6 |
48 |
|
|
48*2 |
48*2.5 |
48*3 |
48*3.5 |
48*4 |
48*4.5 |
48*5 |
48*6 |
50 |
|
|
50*2 |
50*2.5 |
50*3 |
50*3.5 |
50*4 |
50*4.5 |
50*5 |
50*6 |
54 |
|
|
|
54*2.5 |
54*3 |
54*3.5 |
54*4 |
54*4.5 |
54*5 |
54*6 |
60 |
|
|
|
60*2.5 |
60*3 |
60*3.5 |
60*4 |
60*4.5 |
60*5 |
60*6 |
65 |
|
|
|
|
65*3 |
65*3.5 |
65*4 |
65*4.5 |
65*5 |
65*6 |
75 |
|
|
|
|
|
75*3.5 |
75*4 |
75*4.5 |
75*5 |
75*6 |
76 |
|
|
|
|
|
|
76*4 |
76*4.5 |
76*5 |
76*6 |
89 |
|
|
|
|
|
|
|
|
|
89*6 |
Note: We could produce other sizes as your requirements. Surface Treatment: Bright, Galvanized, Phosphated etc. |
Chemical Composition
Steel Grade |
C |
Si |
Mn |
P |
S |
Al |
|
Name |
No. |
max |
max |
max |
max |
max |
max |
E215 |
1.0212 |
0.1 |
0.05 |
0.7 |
0.025 |
0.015 |
0.025 |
E235 |
1.0308 |
0.17 |
0.35 |
1.2 |
0.025 |
0.015 |
— |
E355 |
1.058 |
0.22 |
0.55 |
1.6 |
0.025 |
0.015 |
— |
ST35 |
1.0308 |
0.17 |
0.35 |
0.4(min) |
0.025 |
0.025 |
— |
ST45 |
1.0408 |
0.21 |
0.35 |
0.4(min) |
0.025 |
0.025 |
— |
ST52 |
1.058 |
0.22 |
0.55 |
1.6 |
0.025 |
0.025 |
— |
Mechanical properties
Steel Grade |
Yield Strength (Mpa) | Tensile Strength (Mpa) | Elongation(%) | |
Name |
No. |
ReH (min) | Rm(min) |
A(min) |
E215 |
1.0212 |
215 |
290 to 430 |
30 |
E235 |
1.0308 |
235 |
340 to 480 |
25 |
E355 |
1.058 |
355 |
490 to 630 |
22 |
ST35 |
1.0308 |
235 |
340 to 480 |
25 |
ST45 |
1.0408 |
255 |
440 to 570 |
21 |
ST52 |
1.058 |
355 |
490 to 630 |
22 |
Tolerance
OD |
Allowable tolerance |
Special Tolerance |
||
|
GB/T3639 |
DIN2391 |
OD |
WT |
4mm-20mm |
±0.10mm |
±0.08mm |
±0.05mm |
±0.05mm |
20mm-30mm |
±0.10mm |
±0.08mm |
±0.08mm |
±0.08mm |
31mm-40mm |
±0.15mm |
±0.15mm |
±0.10mm |
±0.08mm |
41mm-60mm |
±0.20mm |
±0.20mm |
±0.15mm |
±0.15mm |
61mm-80mm |
±0.30mm |
±0.30mm |
±0.20mm |
±0.20mm |
81mm-120mm |
±0.45mm |
±0.45mm |
±0.30mm |
±0.30mm |
Delivery Condition
Designation |
Symbol |
Description |
Cold finished (hard) | BK(+C) | Tubes do not undergo heat treatment following the final cold forming and, thus, have a rather high resistance to deformation |
Cold finished (Soft) | BKW | The final heat treatment is followed by cold drawing involving limited deformation. Appropriate further processing allows a certain degree of cold forming (e.g. bending, expanding) |
(+LC) | ||
Cold finished and stress-relieved | BKS(+SR) | Heat treatment is applied following the last cold forming process. Subject to appropriate processing conditions, the increase in the residual stresses involved enables both forming and machining to a certain degree. |
Annealed | GBK(+A) | The last Cold forming process is followed by annealing in a controlled atmosphere. |
Normalized | NBK(+N) | The last cold forming process is followed by annealing above the upper transformation point in a controlled atmosphere. |
Quality Assurance
1.Strict according to DIN2391/EN10305 or other standards.
2. Sample: Sample is free for test.
3. Tests: Salt spray test/Tensile test / Eddy current / Chemical composition test according to customers' request
4.Certificate: IATF16949, ISO9001, SGS etc.
5.EN 10204 3.1 Certification
Application
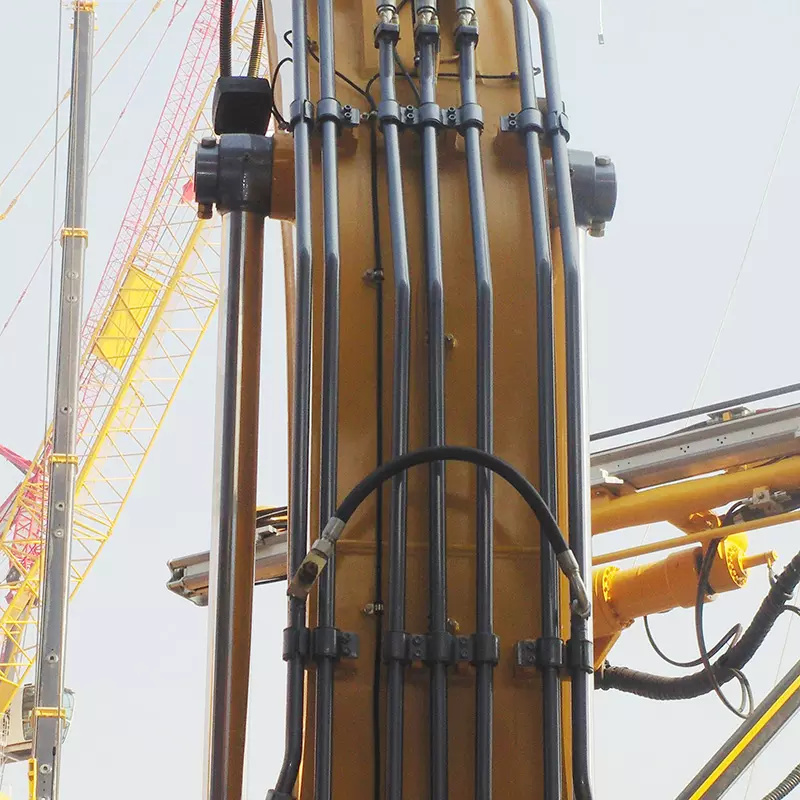
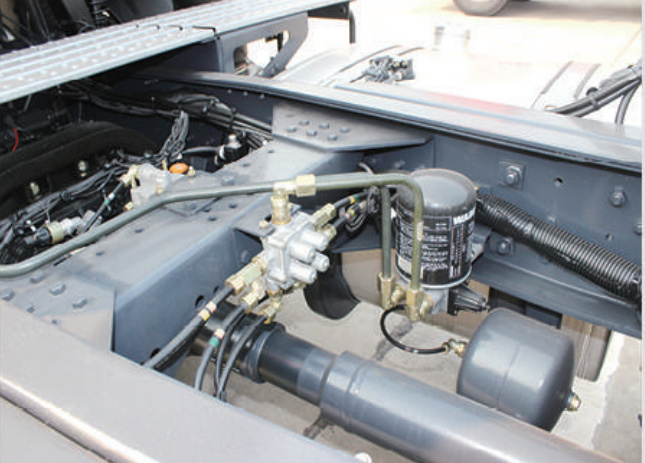