Precision phosphated pipe is a new type of wear-resistant pipeline, which uses the spinning nesting composite technique. It is formed by the mechanical function of spinning nesting composite of two different raw material metal materials together, scientifically utilizing the outer base pipe wall thickness to bear the working pressure of the pipeline system, and using the lined corrosion-resistant alloy pipe to bear the corrosion requirements of the pipeline system.
Compared with traditional wear-resistant alloy cast iron, wear-resistant alloy cast steel, steel ceramic composite pipe, and cast stone pipe, this precision phosphated pipe has the following advantages.
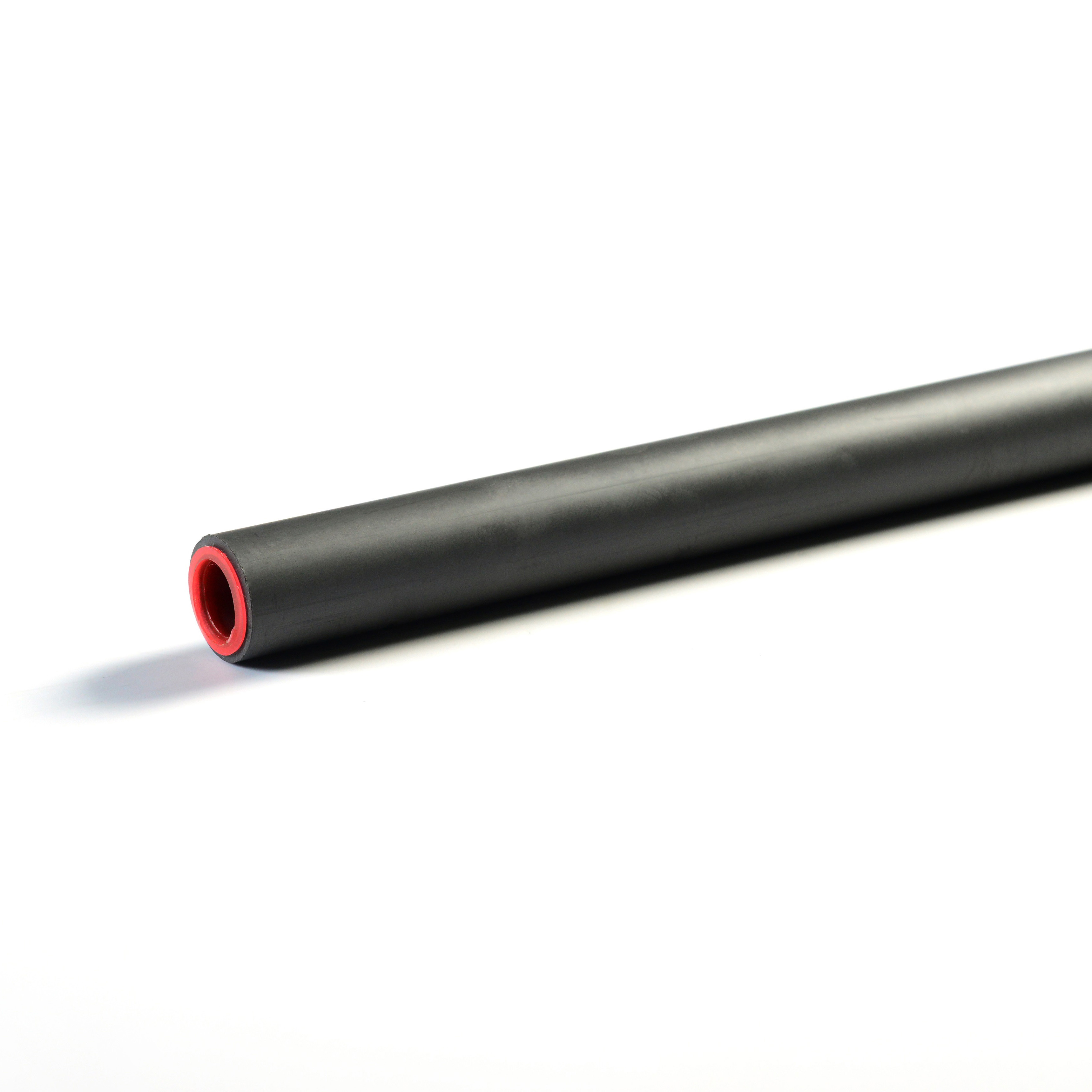
1. Good wear resistance.
2. High pressure resistance, suitable for high pressure levels.
3. The inner lining is tightly combined with the outer steel pipe, and a special process is selected to form a fusion joint between the composite layers, ensuring operational reliability.
4. It has good resistance to mechanical shock and thermal shock.
5. Convenient device connection. Flanges and flexible joints can be used for connection, and can be cut or welded at will.
Scope of use:
Coal powder conveying system, wet dry ash conveying pipe, and stone coal system in thermal power plants
Other pneumatic conveying systems for powder particles
Hydraulic slag transportation system and slurry transportation with larger particle size
Transportation of various mining materials
1. Phosphating effect
(1) Effect of phosphating before coating
① Enhance the adhesion between the coating layer (such as paint coating) and the workpiece.
② Improve the corrosion resistance of the surface coating of the workpiece after coating.
③ Improve decoration.
(2) Effect of non coating phosphating
① Improve the wear resistance of the workpiece.
② Ensure smoothness of the workpiece during machining.
③ Improve the corrosion resistance of the workpiece.
2. Application of phosphating
Steel phosphating is mainly used for corrosion protection and as a base film for paint.
(1) Phosphating film for corrosion protection
① Protective phosphating film is used for corrosion protection treatment of steel parts. The type of phosphating film can be zinc or manganese. The mass per unit area of the membrane is 10-40 g/m2. Apply anti rust oil, grease, wax, etc. after phosphating.
② Phosphating film for paint substrate
Increase the adhesion and protection between the paint film and steel workpieces. The type of phosphating film can be zinc based or zinc calcium based. The unit area mass of the phosphating film is 0.2-1.0 g/m2 (used for the bottom layer of paint on large deformation steel parts); 1-5 g/m2 (used for the bottom layer of paint on general steel parts); 5-10 g/m2 (for the paint base layer of steel parts that do not undergo deformation).
(2) Phosphate coating for cold working smoothness
The film weight per unit area of steel wire and welded steel pipe drawing is 1-10 g/m2; The film weight per unit area of precision phosphating tube drawing is 4-10 g/m2; The film weight per unit area of cold extrusion forming of steel parts is greater than 10 g/m2.
(3) Phosphate coating for reducing friction
Phosphating film can reduce friction. Generally, manganese based phosphating is used, and zinc based phosphating can also be used. For workpieces with small dynamic fit gaps, the mass of the phosphating film is 1-3 g/m2; For workpieces with large dynamic fit gaps (gearbox gears), the mass of the phosphating film is 5-20 g/m2.
(4) Phosphate coating for electrical insulation
Generally, zinc based phosphating is used. Used for silicon wafer phosphating treatment in motors and transformers.
Post time: Aug-24-2023